Driving forward electrification with battery technology
Helping you develop next generation battery materials technology

Electrification of transportation
The battery market is shifting gear to meet unprecedented electric vehicle (EV) demand in the next few years.
Innovation is needed to transform the current lengthy, complex and expensive process to manufacture batteries. Companies who can optimise materials, structures and interfaces, as well as incorporating sensors to maximise performance of batteries stand to gain.

Improving battery recycling
Increased battery usage also presents challenges in managing end-of-life processes for batteries to minimise environmental impact. Current rates of recycling are low, with government targets to increase recyclability in place to drive innovation in resource-efficient technology to enable recovery, re-use and recycling of EV batteries.
Support to transform battery materials
Can your battery materials technology be improved in order to make manufacturing more streamlined and simplified leading to higher volume and sales while reducing costs?
Are you developing reuse or recycling technology to improve the sustainability of batteries and the scarce materials used to produce them?
Improving battery efficiency

Making your battery more efficient has the potential to reduce costs, increase life-span, improve power, range and safety, and to ultimately transform the EV market.
Our approach ensures we can work with you to rapidly meet these challenges by designing and developing prototypes to evaluate and scale-up your technology.
How do we make this possible?
By collaborating with companies of all sizes using our industry relevant expertise and assets we can accelerate and optimise your battery material, formulation or coating with reduced risk.
Optimising battery materials
Our industry-relevant expertise in optimising and developing scalable processes for existing and next generation electrode materials; materials for solid-state batteries; and the recovery of high-value battery electrode materials gives you confidence in your material and formulation decisions.
Interfaces within the battery cell are critical for the performance, durability and safety of the battery. We support this with know-how of surface engineering of materials and device structures.
The ability to investigate new solvent systems is key for manufacturing and to meet future regulations, and we can support you in the selection of such candidate systems using our know-how and assets in high-throughput screening.
Maximising performance through materials processing
Our state-of-the-art capability supports the development and optimisation of battery materials processing. We can assist you in optimising electrode slurry processing using a wide range of mixing technologies to maximise performance. We have industrially relevant wet coating technologies, such as roll-to-roll slot die, to ensure slurry formulations will run seamlessly at scale.
Depositing protective coatings on materials is a key process in enhancing battery life cycle as it has the potential to provide improved longevity and a higher energy density. We have unique vacuum coating technologies which have been shown to improve stability and prevent dendritic growth.

Integrating smart sensors for battery management systems
Enhanced battery management systems (BMS) allow for optimised cell usage and efficiency, reducing the stress experienced by individual cells through their operating life. We have rapid pick and place electronics integration capability that enables us to work on projects to embed sensors on or within individual cells in cost effective processes. Our capabilities in electronics and formulation enables innovative integration of printed electronics on a reel combining pressure and temperature sensors, circuitry, processing, and communications. This creates new form factors for electronics for BMS and offers significant design freedoms. We can help you to develop integrated and multifunctional smart sensors for high-performance battery management solutions, as well as individual cell level monitoring.

Support for recovery, re-use, recycling and life-cycle analysis
With our combined capabilities in process chemistry and electronics we can optimise materials to improve the re-use and recyclability of batteries, creating product differentiation.
We can work with you to explore chemical or synthetic route alternatives to ensure compliance with occupational and emerging environmental restrictions, and support you to develop processes for the recovery of high-value battery electrode materials leading to another supply of materials through reuse.
To make batteries more readily reusable, we can use our capabilities in embedding wireless connected sensors in cells, which provide feedback on a cell’s usage and ‘health’. This data can inform lead to informed decisions around second life applications and has the potential to drive both economic and environmental gains.

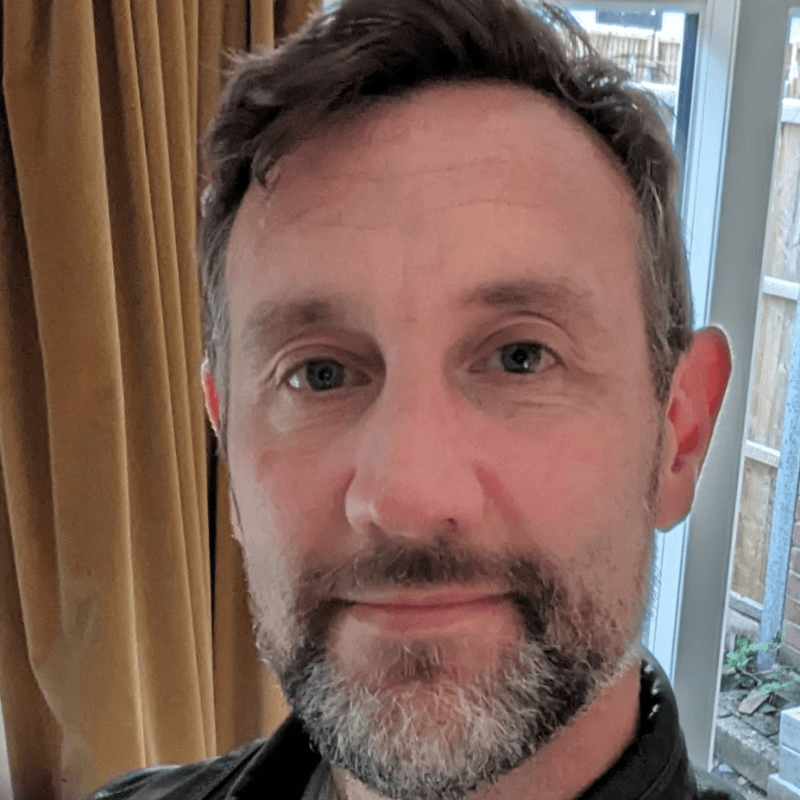