Unclogging the medicine manufacturing bottleneck
Continuous direct compression could cut tablet production from weeks to days, putting life-saving medicines into patients’ hands faster. Here’s how.
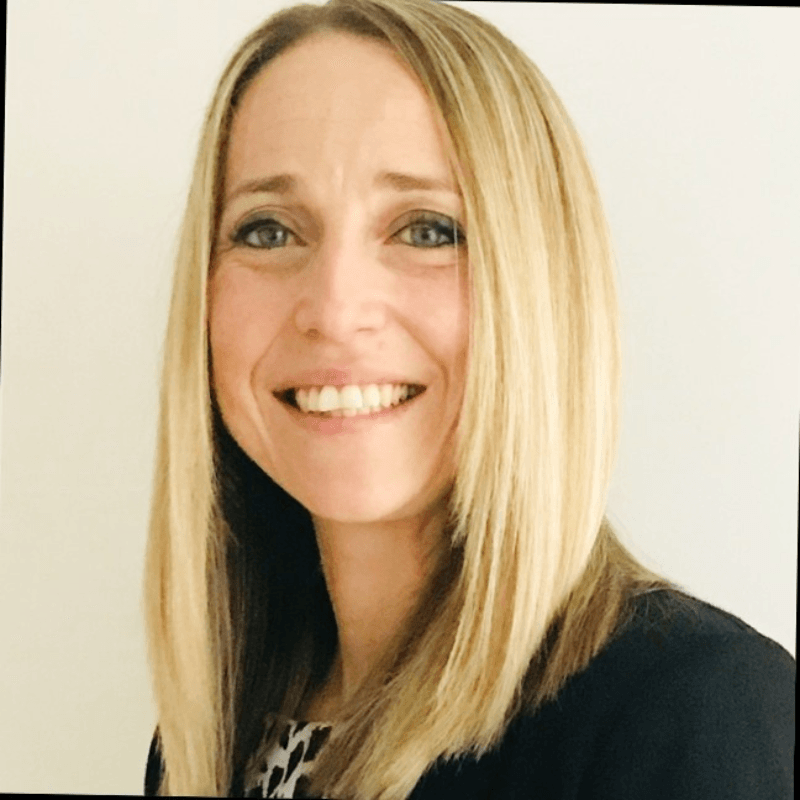
Grand Challenge Lead
(she/her)
Medicines manufacturing typically takes 10 to 15 years to go from discovery to market. That timeline often means patients are left waiting for life-saving treatments.
However, COVID showed that, when there is an urgent threat or pressing need, the pharmaceutical production line can crank into high speed. Whilst lots of attention has been given to the rapid development of COVID vaccines, the same was true for drug production.
According to McKinsey, this was made possible by the alignment of several critical factors; a pandemic-specific regulatory landscape, widely available knowledge of the disease, technological advancement, investment despite the financial risks, operational excellence and innovation in execution. Oral antiviral drugs like the combination nirmatrelvir and ritonavir (Paxlovid) were fast-tracked through discovery and development on the back of existing infrastructure, experience and streamlined production processes.
The pandemic experience highlighted that there are ways to speed up all facets of medicines manufacturing. It also showed the impact of streamlining the physical production process itself. In tablet production, continuous direct compression (CDC) can make a big impact. Faster and more efficient medicines manufacturing improves patient access and affordability, while enabling the industry to lower its environmental footprint.
Large-batch manufacturing is time consuming
Typically, drug production relies on inefficient time and resource-intensive large-batch manufacturing methods that haven’t changed in over 40 years. Batch manufacturing can take weeks to complete a single production run from start to finish. There are several reasons why this process takes a long time:
- A start and stop process. Batch manufacturing is done in a series of sequential steps and each one is carried out as a separate operation, whether that is blending the raw materials, producing the final formulation or packaging the finished drug.
- Interruptions for quality control. After each of the above stages, the process must be stopped to perform quality control checks before moving to the next step.
- Material transfer between rooms or equipment. After each step the materials may need to be moved to another piece of equipment, a new room or even a new site for the next task to be completed. These may need to be cleaned, sterilised, or reconfigured between batches.
There are other considerations too. Batch production often requires storing large amounts of materials, which needs more physical space and can lead to additional time spent on inventory management and storage.
This is amplified when batch processes are scaled up for larger production volumes. Adjusting and optimising manufacturing parameters may take more time, as well as exponentially more resources and space, both for the working process and storage.
This has worked for a medical system that has traditionally been built on a “one-size-fits-all” approach to treatment. However, with the advent of tools that enable precision medicine, personalised treatments and therapies for rare diseases, the pharmaceutical industry must be more agile, flexible and able to cope with smaller volumes and fluctuating demand.
The benefits of continuous direct compression
The increasingly personalised nature of medicine — made possible through greater understanding of the genetic and molecular basis of diseases — requires new, complex drugs to treat clearly identified smaller populations of patients. That places a different onus on the pharmaceutical industry.
Continuous direct compression (CDC) drastically transforms oral solid dosage (OSD) tablet production. In a continuous flow, the raw materials are fed into production and final products are produced. Shorter runs of tablets, with much lower amounts of active pharmaceutical ingredients (APIs), pass through streamlined processes where multiple steps are integrated. Monitoring and adjustments can also be carried out in real time. This results in faster production times, improved quality control, and lower costs. Crucially, it enables life-changing and life-saving drugs to get to more patients quicker.
Reducing resource and energy consumption is also a step towards a greener pharma industry.
Based on our experience, CDC enables a:
- 60 – 70% reduction in facility size
- 30 – 50% reduction in manufacturing costs
- 69% reduction in energy consumption
Embedding CDC into pharma
Despite the enormous benefits of CDC, which reduce time to market and increase revenue, only 13 products have been approved for commercial use. Pharmaceutical companies set up for large-batch manufacturing may be put off by the upfront costs or the regulatory hurdles that come with continuous small or mini-batch processing.
At CPI we are pioneering CDC by helping partners prove it is viable for producing their product at commercial scale. We do this by bringing together partners from academia and industry at our Medicine Manufacturing Innovation Centre. The facility operates as a good manufacturing practice (GMP) environment and houses a physical demonstrator where partners put their product through the process.
In addition, we offer digital twin modelling facilities for partners to predict both batch and continuous compression processes. This helps scientists better understand and optimise their equipment and process in a digitally modelled virtual space, allowing them to take their insights into production without wasting precious resources on physical experiments.
Using CDC to go from drug prototype to commercial-scale product creates better scale-up efficiencies, greater quality assurance and quickens the speed into the clinic. That ultimately serves the people who most need it: patients and their families.
Explore how CPI can help you implement CDC in your drug production line. Schedule a free consultation with our experts today.
For more information
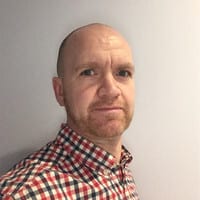
Enjoyed this article? Keep reading more expert insights...
CPI ensures that great inventions gets the best opportunity to become a successfully marketed product or process. We provide industry-relevant expertise and assets, supporting proof of concept and scale up services for the development of your innovative products and processes.