The Diversity and Synergies of Formulated Products
CPI consultant David Smith explains how formulated products that seem quite different on the surface, can have surprising process synergies
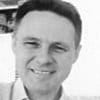
Consultant
For many people the words “formulated” or “formulae” conjures to mind images of mad scientists mixing coloured bubbling liquids to produce magical concoctions. At the very least, formulations are perceived as related only to medicines. Nothing could be further from the truth and it never ceases to amaze me how the connections between formulated products are so many and diverse.
What is a formulated product? Quite simply it is any product that is composed of a mixture of raw materials that have been designed in specific proportions to impart certain desired properties to the final material mixture. Chemical reactions are sometimes involved although in most formulated products the characteristics of the finished product are purely due to the physical interactions between the individual components. For example, the non-drip behaviour of a paint is created by the physical interaction of a thickener component with the other ingredients.
Formulated products are extremely diverse and include cosmetics, pharmaceuticals, pesticides, processed foods, detergents and paints. It is estimated that the combined global market for formulated products is around $1000bn. The development and manufacture of formulated products adds significant value above the cost of the raw materials, with a value multiplier ranging anywhere from 3 – 100 compared to the raw materials.
I have illustrated the obvious diversity in formulated products but what of the synergies, where do they lie and why does it matter? The most obvious critical step in the development of a formulated product is the role of a formulator in deciding which materials are required to achieve the desired function of the finished product. For example, in the development of a laundry detergent powder, the selection of the chemicals required to perform the bleaching and cleaning of the clothes. However, what is less obvious, is the engineering technology that is necessary to deliver the chemistry to the consumer in the required final product form e.g., powder, tablet or gel. Most importantly this must be via an efficient manufacturing process so that the consumer can enjoy the product at an affordable price and the producer makes a profit. It is in this area, the process engineering, where the synergies are to be found across the diverse range of formulated products.
Here I will explain how an alkaline disposable battery and the ‘mint with a hole’ share a surprising link. Quite clearly, the composition of a disposable battery and a mint have nothing in common but the process engineering of these products have many similarities. Mints such as Polo® mints are produced on tablet presses. The starting point is a powder mixture with the right physical properties required to produce a tablet with enough strength to survive packaging and handling. But it must not be too strong for biting and delivering flavour in the mouth. Both these parameters are linked to the tablet porosity and the compression force in the tablet press. This is almost the same formulation and process engineering challenge as faced in the development of pharmaceutical tablets. Here an appropriate balance must be struck between tablet strength for handling and not making it too hard so as to slow down the rate of drug absorption in the stomach. But, you may ask, what about batteries and mints?
A Polo® mint is produced on a special type of tablet press that enables the tablet to have a hole in the middle. A modern alkaline battery is composed of a compressed ring of cathode powder that surrounds the anode material. The cathode is a compressed powder, and exactly like a Polo® mint it is produced on a tablet press using a powder manufactured with the specific characteristics to produce a tablet with the right properties. For a battery, the cathode “tablet” must be hard enough for physical handling (e.g., insertion into the battery casing) whilst having enough porosity to enable the chemical reactions to produce a current.
So, the process engineering principles and product characteristics for a Polo® mint and the cathode of a battery are virtually identical as to intent, just differing in the final purpose for the tablet as illustrated below.
You may be thinking that’s interesting but so what? The development of formulated products and the design of efficient manufacturing processes is an extremely time consuming and costly undertaking. The above example illustrates how knowledge gained in apparently unconnected industries may be very valuable to share, with the common goal of building the knowledge base on the processes used to make formulated products.
CPI’s National Formulation Centre is ideally placed to facilitate this aim by bringing together industries using common process technologies and by forming a knowledge hub. CPI offers lab and pilot scale capabilities as well as technical expertise in the most common synergistic areas of process technologies. These technologies have the breadth of applicability across market sectors as illustrated by the example of mints and batteries, but also across technologies which integrate closely with formulation such as industrial biotechnology, printable electronics and biologics.
Companies of all sizes can access the state of the art lab and pilot plant facilities. In conjunction with access to technical experts, this will enable faster and cheaper development of new formulated products. This is great news to consumers and to the formulated products industry who can bring innovation to market quicker and at lower cost.
Enjoyed this article? Keep reading more expert insights...
CPI ensures that great inventions gets the best opportunity to become a successfully marketed product or process. We provide industry-relevant expertise and assets, supporting proof of concept and scale up services for the development of your innovative products and processes.