How Quality by Design can improve your product packing
How Quality by Design can make and package formulated products, improving customer satisfaction and bottom lines.
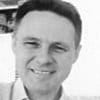
Consultant
The manufacture of formulated products ranging from detergents to pesticides involves a high investment in both time and equipment to ensure that the bulk product is produced according to specification.
However, did you realise that final quality can be severely compromised by the process of putting the bulk product into the final consumer pack?
This is compounded by the fact that for non-regulated products, the amount of check quality sampling & analysis is typically in the region of 1 pack in 10,000 and therefore whilst quality may be at target on average, there could be as much as 50% of packs out of limits for one or more key quality attributes.

Financial constraints on analytical labs and labour costs mean that it is simply not possible to perform traditional analytical methods on a high proportion of packed product. How then to solve the problem of ensuring that the product quality is on target in every pack? After all, it only takes one bad experience for your consumer to stop buying your product.
Figure 1 below shows the typical key process elements (in red) of most packing lines for powder products. This process divides the bulk blended product into the correct dosage for each pack. This could be a box of washing powder or a single use capsule of coffee. Assuming that the bulk blended product is of the right quality, it may be surprising that an apparently simple operation of dosing the product into a pack can so severely impact pack to pack quality.

Three factors will impact the quality in each pack:
The development of knowledge that enables the deployment of process control approaches to ensure that product quality is kept within limits is called Quality by Design.
In recent years Quality by Design has been a hot topic in the pharmaceutical industry under the banner of “process analytical technology” or PAT. PAT has been defined by the United States Food and Drug Administration (FDA) as a mechanism to design, analyse, and control pharmaceutical manufacturing processes through the measurement of Critical Process Parameters (CPP) which affect Critical Quality Attributes (CQA). The concept of PAT is equally applicable to the manufacture of a powdered soup drink as it is to pharmaceuticals.
Firstly as Quality by Design requires data to develop the necessary understanding of the process and product interactions CPI provides the facilities and tools to collect such data.
Fig. 4 illustrates a new powders pack filling line currently being built for CPI by All-Fill International Ltd. with advanced on-line instrumentation from Innopharma Technology (see fig. 3). This facility will be available for use at CPI’s new Netpark National Formulation Centre from early 2018.
The facility has been specifically designed to provide a high degree of process and on-line product quality instrumentation/PAT tools fully compliant to Industry 4.0 standards of digital connectivity. The setup is based on a “plug and play” concept enabling easy testing of different equipment options and configurations.
Secondly CPI can help with the physical material properties having created a state of the art powder characterisation lab with access to the most innovative tools to assess material properties such as the Freeman FT4 powder rheometer (see fig. 2).

Thirdly CPI facilities companies in testing existing and new tools in a realistic manufacturing environment.
On-line measurement for fluids is an order of magnitude simpler than with solids since the presentation of the sample probe to the material rarely represents a significant challenge due to the continuous homogenous nature of fluids.
However, the discontinuous nature of solids creates many practical issues regarding the specific method of instrument installation so that a reliable and representative measurement is ensured at all times. The instrumentation capabilities installed on the packing & filling line at CPI, represent state of the art and best practice for installation. Companies can test the benefits of these tools and also use CPI to test new formulations/products/processes in a realistic manufacturing environment.
The Packing and Filling capability being created at CPI is a state of the art process capability with a high level of digital instrumentation for both process conditions and product quality outputs.
Coming online in early 2018, the facility will be open for business to help industry solve pack filling challenges. Creating more efficient sustainable packing processes which deliver consistent on target product quality to the end user.
Enjoyed this article? Keep reading more expert insights...
CPI ensures that great inventions gets the best opportunity to become a successfully marketed product or process. We provide industry-relevant expertise and assets, supporting proof of concept and scale up services for the development of your innovative products and processes.