Accelerating drug production with “just-in-time” manufacturing
“Just-in-time” manufacturing makes drug production faster, flexible and less wasteful, getting vital medicines to patients quicker.
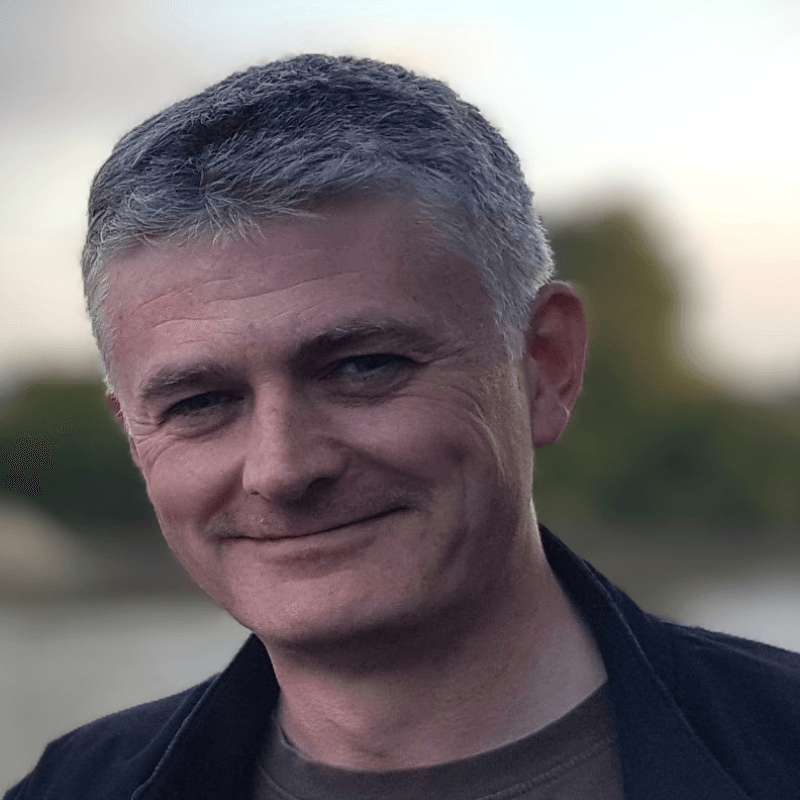
Grand Challenge Lead
(he/him)
In 2021, the UK government proposed legislative changes to speed up clinical trials and get life-changing drugs to patients more quickly. It was backed up by an independent review in 2023 that made further recommendations, including reducing turnaround time for clinical trial approvals and getting studies up and running more quickly.
Pre-COVID, pharmaceuticals production relied on a “just-in-case” (JIC) manufacturing model where batches are prepared and stockpiled. The industry has been hesitant for medicines manufacturing to transition away from this production model due to the resources already invested in it and the up-front cost of moving to a new one. But, during the pandemic, governments and the pharmaceutical industry recognised that flexibility and speed were paramount. Speed and flexibility are two of the main benefits of making medicines using a “just-in-time” (JIT) approach, where only enough medicine is made to satisfy current demand.
Making JIT a part of medicines manufacturing is the goal of our Grand Challenge 2 at our Medicines Manufacturing Innovation Centre because it removes many of the obstacles, costs and waste associated with drug manufacture, especially for clinical trials.
The benefits of “just-in-time” production
In JIC manufacturing, pharmaceutical products are produced in large batches. Production is overestimated, sometimes by as much as 20%, to account for supply chain issues or delays in trial recruitment that result in the expiry of the stock. Although this allows the manufacturer to absorb market demand, it also often leads to wastage of medicines at the end of a trial, known as ‘overage’, which can be as much as 50 or 60% of the total they produce.
The packaging and labelling of such a large stock also means that these drugs are committed to specific studies, sites or countries from the beginning. On top of that, the whole process is expensive, and a large amount of space is needed for both production and storage.
JIT production, on the other hand, is a more agile, responsive and lower-cost method for medicines manufacturing. Not only can new batches of product be quickly produced in response to an uptick in demand, they can also be packaged and labelled for clinical trial sites wherever needed, or for trials in new countries. It even allows last-minute labelling before the supply is sent to its destination. This means vital medicines can be put into the hands of patients much faster.
For manufacturers, little to no stock is held as inventory, so the production and storage capacity required is vastly reduced. There is also less risk and capital wrapped up in materials that could become damaged or expire in storage, resulting in fewer wasted medicines overall. This could greatly benefit SMEs operating within tight financial margins.
Another benefit is that drugs can be supplied direct-to-patient as necessary. The “direct-to-patient” production and supply model – critical during the pandemic – encourages clinical trial recruitment and retention as patients don’t have to leave their homes to receive the medicines.
So, with all these benefits, how can we help the pharmaceutical industry test out a JIT model to facilitate the transition to a more agile medicines supply chain?
The PACE line: packaging drugs “just-in-time”
CPI’s PACE (Pharmacy Automation for Clinical Efficiency) line platform is a digitally enabled, automated line, interfacing novel hardware with innovative software, housed within the Medicines Manufacturing Innovation Centre. It brings the production, packaging and labelling of multiple drugs under one roof without cross-contamination.
Once drugs have been formulated ready for production, possibly through a continuous small or mini-batch process, they are ready for the PACE platform’s automated bottle packaging line. The full line comprises handling, filling, sealing, weighing, marking, labelling, and packing of tablets and capsules with custom amounts of drug compounds.
The drugs pass through a modular filling station with a series of independent humidity and temperature-controlled drug filling stations. This enables a single line to quickly change between multiple drug products – for example to dispense tablets or capsules of differing types and strengths into bottles or fill finish the drug formulation directly into vials for labelling or packaging.
Once packed, the bottles are sealed and stored with a customised bar code that enables rapid labelling. It also provides a cost-effective option for labelling and distribution to individual patients.
All the processes involved are done on a single line without cross-contamination in a good manufacturing practice (GMP) environment, where quality control teams and qualified persons (QPs) can meticulously monitor quality via a dashboard in real-time and then release batches. Any bottle or vial that fails these checks is rejected and logged so the order can be fulfilled as soon as possible.
A faster turnaround for future medicines
Developing the pharmaceutical supply chain of the future requires increasing speed, flexibility and efficiency in clinical trial drugs manufacture. A streamlined clinical supply that incorporates a digitally automated JIT approach to manufacturing with real-time analytics, such as the PACE line, can drastically reduce drug development lead times, logistics, waste and costs. This approach enables manufacturers to optimise their clinical supply chain, making them more agile and able to deliver truly responsive, demand-driven medicines;
The potential to slash production timelines from hundreds of days to less than a month is a game-changer that promises delivery of life-saving treatments to patients faster – and with a smaller environmental footprint. This makes JIT a compelling proposition for the industry.
The PACE line provides a pathway for adoption of JIT manufacturing within the pharmaceutical industry that will not only propel the sector by speeding up time to market, but ultimately also create a healthier society and more robust economy.
Discover how PACE can transform your supply chain and find out how to become a partner:
For more information
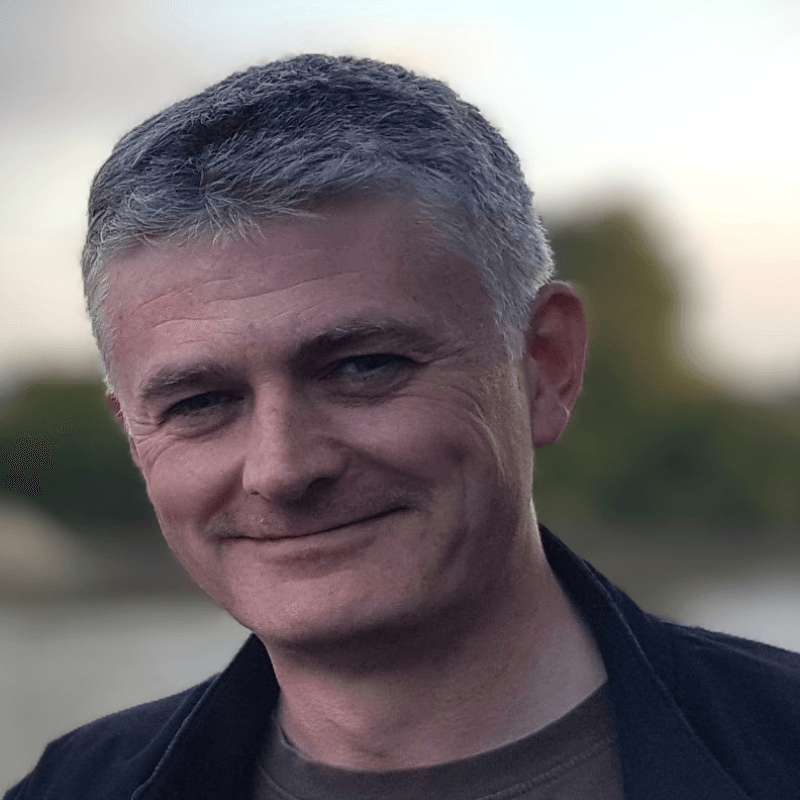
Enjoyed this article? Keep reading more expert insights...
CPI ensures that great inventions gets the best opportunity to become a successfully marketed product or process. We provide industry-relevant expertise and assets, supporting proof of concept and scale up services for the development of your innovative products and processes.