Producing oligonucleotides sustainably
Developing revolutionary manufacturing processes for more sustainable, large-scale production of oligonucleotide therapeutics
Summary
The advent of low-cost gene sequencing, genetic disease mapping and DNA and RNA synthesis has generated a surge of interest in oligonucleotide therapeutics. These short, chemically synthesised fragments of DNA or RNA target the production of proteins significant in disease.
Oligonucleotide therapies are already approved for use in multiple rare genetic disorders and have the potential to help treat more common and chronic diseases, like Alzheimer’s and high blood pressure.
The oligonucleotide therapeutics market is expected to be worth $8bn by 2026. However, it is difficult to produce oligonucleotides easily, cheaply and at scale using current technologies. This poses a challenge to making these life-changing therapies available to everyone who needs them. The goal of industry Grand Challenge 3 is to develop a sustainable, scalable and cost-effective manufacturing process for oligonucleotide-based medicines, this has paved the way for the creation of the Oligonucleotide Manufacturing Innovation Centre of Excellence at the Medicines Manufacturing Innovation Centre,
Oligonucleotide therapeutic manufacturing
Oligonucleotides are currently manufactured in a complex, material-intensive and time-consuming process that involves cyclically adding nucleotides to an anchored oligonucleotide chain (solid phase synthesis) and then purifying the product using chromatography. This final purification step contributes roughly 40% of raw material and resource use and most of the time in manufacturing and analysis.
Researchers and innovators are aiming to increase capacity by switching from solid phase synthesis, which limits batch size, to liquid phase synthesis. This approach could also reduce solvent usage and decrease manufacturing costs. They’re also exploring the use of enzymes (biocatalysis), which would enable the reaction to be run in an aqueous (water-based) system, removing the need for solvent and reducing or eliminating the final purification step.
Our sustainable oligonucleotide solutions
The Grand Challenge 3 innovation programme brings together oligonucleotide therapy industry leaders to improve manufacturing processes and combat the biggest barriers to scaling up sustainable production.
The project was conceived as part of a wider collaboration between Novartis, the NHS and the UK Government to use the oligonucleotide therapy Leqvio (inclisiran) for treating high LDL-cholesterol. Its goal is to improve patient access to the drug through a supply agreement, advancing clinical trials, and addressing the manufacturing challenges that inclisiran, and other large patient population oligonucleotide therapies, will face.
The Grand Challenge objectives are to:
- Develop and demonstrate technology to improve patient access.
- Scale oligonucleotide manufacture to greater than 5 metric tonnes per year.
- Significantly reduce cost.
- Enhance environmental sustainability.
The programme consists of two core projects: Nanostar and Biocatalysis. These projects were funded by Innovate UK and the industrial collaboration partners for Nanostar are AstraZeneca, Novartis and Alnylam and technology partners Exactmer. Partners for Biocatalysis are Novartis, AstraZeneca, Novo Nordisk, BioMarin and The University of Manchester with CPI coordinating and delivering the projects.
Each of the technological solutions offered by our core projects present unique oligonucleotide therapeutic manufacturing benefits:
Nanostar liquid phase synthesis
This approach replaces solid-phase synthesis with liquid-phase synthesis. Exactmer’s Nanostar Sieving™ molecular sieving platform uses advanced membranes to isolate the oligonucleotides and remove by-products of the chain-building cyclical reaction.
For this process to be sustainable, the ratio of raw materials to oligonucleotides produced process mass intensity or PMI) must be measured and optimised.
We are currently calculating the PMI for the Nanostar process, which will help identify where further improvements can be made. After larger pilot-scale batches have been run, the synthesiser will be available for technical trials.
Benefits:
- Scalable, solution-based process.
- Potential to reduces solvent volumes.
- Increases opportunities for solvent recycling.
- Lowers manufacturing costs.
Biocatalysis
Biocatalysis replaces complex chemistry using multiple reagents and enables the reaction to be run in a water-based system, rather than relying on large amounts of harmful solvents. This simplifies the equipment needed for the manufacturing process and increases the purity of the resulting oligonucleotide. We are currently preparing to scale up the lab process with a view to introduction to commercial manufacture
Benefits:
- Removes need for solvent.
- Simplifies process and equipment.
- Increases synthesis product purity, removing the need for chromatography purification and extraction.
- Increases sustainability through decreased resource use: PMI reduced by approximately 7‑fold.
Collaborate with CPI
With many prospective oligonucleotide-based medicines already in development and clinical trials, it is vital to put cost-effective, sustainable and scalable manufacturing methods in place now so that the industry can meet current and future manufacturing needs.
At the Medicines Manufacturing Innovation Centre, we employ a collaborative, pre-competitive operational model that will be replicated at the Oligonucleotide Manufacturing Innovation Centre of Excellence.
The centre also incorporates the RNA Training Academy, which provides training and development opportunities for this highly skilled workforce.
We are seeking new partners to help develop and test these new technological solutions for sustainable oligonucleotide therapeutic manufacture so we can ensure faster access to ground-breaking medicines for the patients who need it most.
Find out more about our sustainable oligonucleotide manufacturing capabilities:
For more information
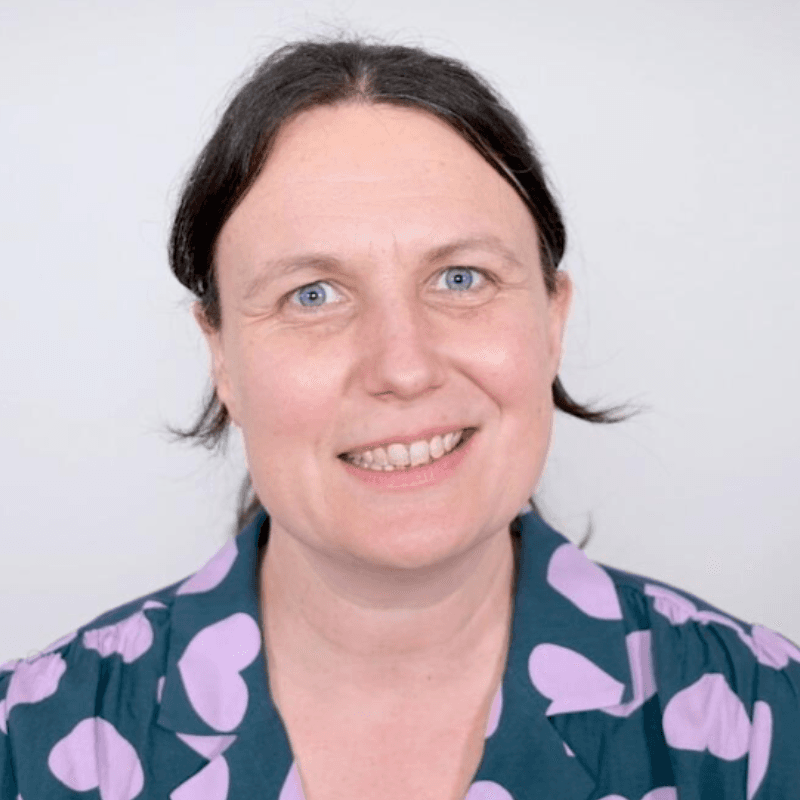
Let’s innovate together
To find out more about how we can work together, please enter your details below.